
“Echt een machine voor het high-tech marktsegment”, zo karakteriseert directeur Nico van Wijnen van gereedschapmakerij ARTooling in Gameren het RP600 HSC-bewerkingscentrum van Röders. De machine werd zeven jaar geleden aangeschaft om aan de steeds hogere nauwkeurigheidseisen te kunnen voldoen en op dat punt heeft de RP600 haar beloftes volledig ingelost. Dankzij de automatische updates van de besturingssoftware is de machine ook nog eens tien procent sneller geworden.
“Dat we nog bestaan komt omdat we een duidelijke strategie hebben”, aldus Van Wijnen. Een van de kernelementen van die strategie is het aanbieden van een totaalconcept aan klanten in het high-end segment van de markt, waarbij ARTooling het hele pakket aan spuitgietmatrijzen en stempels rond een eindproduct voor zijn rekening neemt. Hij noemt als voorbeeld een koffiezetapparaat waarvoor zowel de stansgereedschappen voor de metaaldelen als de spuitgietmatrijzen voor de kunststofdelen worden vervaardigd.
En hoewel Van Wijnen opmerkt dat de projectvoering bij dit soort opdrachten nog belangrijker is dan het maakproces zelf, daar aan de bovenkant van de markt gaat het onvermijdelijk ook om de laatste micrometers. Met name in een kritisch segment als de medische industrie, waar het onderste uit de fijnmechanische kan gehaald moet worden. Van Wijnen laat een medisch instrument zien met injectienaalden, waarbij de buitendiameter … bedraagt en de opening een diameter heeft van …. Dat lukt alleen wanneer de toleranties binnen heel nauwe marges beheerst worden. Nauwkeurigheden op een dergelijk niveau vragen om machines met een onberispelijke reputatie op het gebied van stabiliteit en betrouwbaarheid.
Spindelsensor
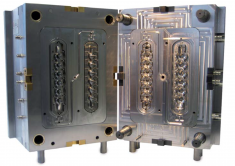
Stijfheid en stabiliteit zijn belangrijke kenmerken van de Röders machines. Directeur Theo Coffeng van Dymato in Veenendaal, sinds begin 2009 de vertegenwoordiger van Röders in Nederland, noemt in dat verband onder meer de portaaluitvoering, waarbij het bed de X-beweging voor zijn rekening neemt en de kolom de Y- en Z-beweging. In verhouding met andere oplossingen biedt dat volgens hem niet alleen voordelen wat de stabiliteit betreft, maar het geheel aan bewegingen dat nodig is om een product te bewerken ligt verhoudingsgewijs eveneens lager. Ook de uitsteeklengte van het gereedschap is zo laag mogelijk gehouden om de kans op afwijkingen zo klein mogelijk te houden.
Waar de machine volgens Van Wijnen en Coffeng ook in uitmunt is de correctie van de spindeluitzetting bij temperatuurstijging. De kolom is uitgerust met een sensor die de uitzetting rechtstreeks meet. Dat is nog weer een graadje nauwkeuriger dan een indirecte temperatuurcorrectie. De positie van de gereedschapneus in de Z-richting kan daardoor worden gegarandeerd met een nauwkeurigheid van 2 µm. Alle bewegende onderdelen van de machine worden bovendien gekoeld om temperatuureffecten tot een minimum te beperken.
Juiste spaandikte
Een belangrijk element is voor Van Wijnen ook het hoge toerental tot 38.000 min-1. Op de machine worden zowel hardmetalen onderdelen bewerkt als grafietelektrodes voor de zinkvonkmachines en op beide terreinen kan de machine daarmee uit de voeten. De spil is Vector-gestuurd, wat erop neerkomt dat de machine ook bij lage toerentallen nog voldoende koppel heeft. Met het oog op die grafietelektrodes, waarbij nogal wat stof vrijkomt, wijst Coffeng ook op de stofdichte uitvoering van de machine. Hij spreekt zelfs van een ‘volmaakte afdichting’. Het voorkomt dat door het grafietstof op termijn het functioneren van de machine op het spel komt te staan.
Dat hoge toerental van de Röders gaat hand in hand met een stevige dynamiek. Voor Van Wijnen eveneens een belangrijke element en niet alleen vanwege de productiviteit. “Die dynamiek is nodig om de 3D contouren goed te kunnen volgen”, geeft hij aan. Hij voegt daar nog aan toe: “Om goed te verspanen is een juiste spaandikte van belang. Hoe eerder de juiste snelheid is bereikt hoe beter de oppervlaktekwaliteit en hoe minder slijtage van de gereedschappen.” Vandaar dat de versnelling van 1g dan ook op verschillende aspecten (productiviteit, kwaliteit en slijtage) positief uitwerkt.
Toerentalcorrectie

De kwaliteit en snelheid van de besturing is eveneens essentieel om zowel qua productiviteit als nauwkeurigheid het beste resultaat te bereiken. Om het 3D-contour zo exact mogelijk te kunnen volgen is een hoge reactiesnelheid een voorwaarde. In de vorm van het RMS 6 pakket levert Röders zijn eigen besturingssoftware, met een reactietijd van minder dan 0,1 ms en met een capaciteit om meer dan 10.000 bewerkingselementen vooruit te zien. Dat is van belang bij hoge bewerkingssnelheden. De voedingssnelheden worden bovendien automatisch aangepast aan de vorm van het contour, om op elke positie de maximale nauwkeurigheid en oppervlaktekwaliteit te bereiken.
Het besturingspakket wordt door Röders bovendien telkens automatisch aangepast volgens de laatste versie. Zonder verdere ingrepen wordt dezelfde machine daardoor in de loop der tijd steeds sneller. Het bedrijf geeft zelf als voorbeeld een matrijsdeel voor een flessenbodem, waarvan de bewerkingstijd in de loop van tien jaar met 41 procent is ingekort. Van Wijnen zelf schat de gemiddelde tijdwinst op omstreeks 10 procent voor het hele productenpakket, sinds hij de machine heeft zeven jaar geleden heeft aangeschaft.
Een bijzonderheid van de RMS 6 besturing is nog dat in een vooraf geselecteerde toerentalrange automatisch het optimale toerental wordt gegenereerd. Dat wil zeggen met het minimale vibratieniveau, ook dat draagt bij aan een optimale oppervlakteruwheid.
Hydrostatisch

Van Wijnen heeft destijds bewust gekozen voor een drie-assige uitvoering. “Qua complexiteit van de bewerkingen hebben we eigenlijk een vijfasser nodig, maar dan lever je wel wat in op het punt van nauwkeurigheid”, geeft hij als afweging. Principieel valt daar weinig tegenin te brengen, maar volgens Coffeng haalt Röders bij haar vijfassige machines desondanks een tolerantieniveau beneden 5 µm. “Dat is inderdaad iets ruimer dan de 1 à 2 µm bij drie-assige machines, maar voor de meeste toepassingen toch ruimschoots acceptabel.”
De RP600 bij ARTooling is nog uitgerust met kogelomloopspillen (waarbij de voedingssnelheid kan oplopen tot 30 m/min), sinds 2009 levert Röders haar HSC-machines echter zonder uitzondering met lineaire aandrijvingen (de RXP-serie). “Dat maakt de machines nog dynamischer en qua prijs maakt het nauwelijks verschil meer”, aldus Coffeng. De voedingssnelheden kunnen hier oplopen tot 60 m/min, afhankelijk van het type. Die lineaire aandrijvingen bieden ook nog eens meer nauwkeurigheid, onder meer omdat temperatuureffecten hier niet optreden.
Voor wie de hoogste graad van nauwkeurigheid nastreeft levert Röders daarnaast nog de RHP-uitvoering met hydrostatische blokgeleidingen. Naast frezen, boren en tappen worden deze machines ook ingezet voor het coördinatenslijpen. Zie voor het complete aanbod van Röders: dymato.nl en www.roeders.de.
ART Group: top-3 van Europa
kadertekst: ARTooling, het vroegere GVW, maakt samen met SMS (high-end matrijzen) en WTS (parts en reservedelen), beide in Tilburg, deel uit van de ART Group. De bundeling van krachten kan worden gezien als het resultaat van de zoektocht naar een ‘unieke positie in de markt’. Als uitvloeisel daarvan zijn de partners zich de afgelopen jaren sterk gaan richten op de levering van totaalconcepten aan het topsegment van de markt, waar veel kennis en kunde om de hoek komt kijken. “Rond de matrijzen als basisproduct hebben we een heel kennisblok gebouwd”, aldus Van Wijnen en hij rekent de ART Group inmiddels tot de top-3 van Europa op haar terrein. Zo’n 30 tot 40 procent van de gereedschappen wordt in het buitenland afgezet, tot in Azië.
Om binnen deze complete turn-key projecten de juiste prijs/kwaliteit verhouding te kunnen bieden wordt de aanmaak van een deel van de benodigde matrijzen uitbesteed. Voor de coördinatie daarvan en de bewaking van het Europese normenniveau zijn met name ART Europe en ART Asia in het leven geroepen. Matrijzen voor kritische sectoren als de medische industrie en voor moeilijk te verwerken materialen als glasvezelversterkte kunststoffen worden nog altijd in zijn geheel in Nederland gefabriceerd. Dat geldt ook voor proefproducties en proefpersingen. Voor meer informatie zie www.artooling.com.
Bron: AR Tooling (PDF)