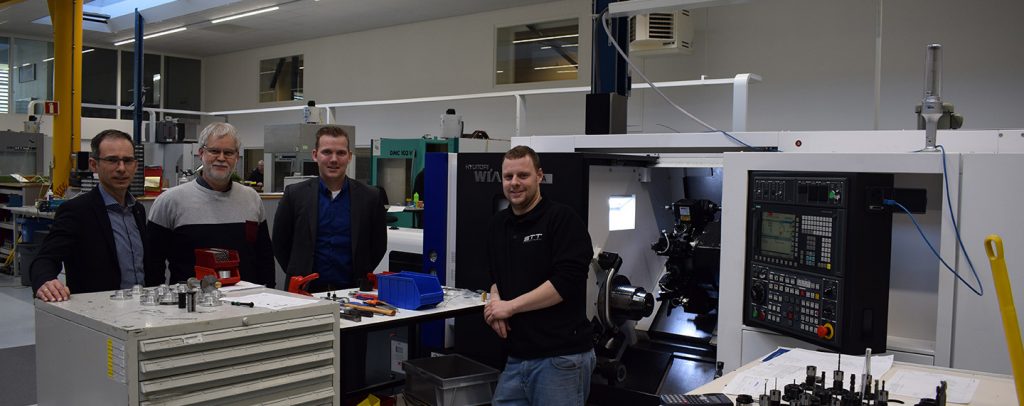
Door hun blik te verbreden is STT Products sinds 2008 weer groeiende. Naast het produceren van speciaalmachines en volautomatische assemblagelijnen, komt er steeds meer toeleverwerk naar het bedrijf in het Groningse Tolbert. Dit vraagt om slim produceren en om de vernieuwing van het machinepark.
STT Products heeft sinds de sluiting van Cordis in 2007, destijds één van de belangrijkste afnemers van het Groningse bedrijf, zich drastisch moeten aanpassen om voort te kunnen bestaan. “Door onze blik te verbreden zijn we snel weer een groeiende onderneming geworden”, vertelt Menno Kooistra, directeur van STT Products. Het bedrijf dat veelal assemblagelijnen en machines voor de glas- en medische industrie produceert, geeft aan actief bezig te zijn met Smart Industry. “Een voorbeeld is de meetoplossing die we met een partner ontwikkeld hebben voor de glasindustrie. Deze van oudsher conservatieve industrie gaat met deze oplossing vooruit lopen op het gebied van slim produceren. Met vision oplossingen wordt veel procesdata verzameld, wat het mogelijk maakt om vroegtijdig te anticiperen op onjuistheden. Daardoor kan er foutloos geproduceerd worden”, aldus Kooistra. Voor de in-line controle worden bijvoorbeeld infraroodcamerasystemen toegepast die meetdata zoals vormsnelheid en temperatuur uit het proces halen.
Slim door werkplaats lopen
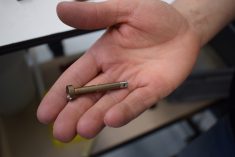
De kennis die STT opbouwt op het gebied van procesoptimalisatie past het ook toe in de eigen productie. De kennis wordt vergaard door werkzaam te zijn voor een vergevorderde industrie, maar ook door samenwerkingen met onderzoeksinstellingen zoals Dekra, TNO en universiteiten. Kooistra vat Smart Industry samen als ‘slim’ door je werkplaats lopen. En dit is in de werkplaats in Tolbert ook doorgevoerd. “Het streven is om constant te blijven optimaliseren en sterk oplossingsgericht te werk te gaan met als uiteindelijk doel om meer uren productief te zijn.” Zo programmeert STT bijvoorbeeld volledig met model based definition in CAD/CAM. De noodzaak van 2D-tekeningen vervalt daarmee en dit scheelt tijd en dus geld voor de engineeringsafdeling. Tevens is automatisering een oplossing waarmee tijdswinst valt te behalen, mits juist ingezet. “We hebben een robotsysteem in gebruik waar standaard bij elke omstelklus veel data moet worden ingevoerd. Onze eigen programmeurs hebben daarom een ‘schil’ over de software geprogrammeerd waardoor de omsteltijd van 1,5 uur is gereduceerd naar slechts 15 minuten.” Dit soort optimaliseringen verhoogt de flexibiliteit en productiviteit van het bedrijf aanzienlijk. En flexibiliteit wordt steeds belangrijker volgens Dirk Woudstra, productiemanager bij STT Products. “Door de alsmaar korter wordende levertijden kunnen we in de fabriek nog maar maximaal vier weken vooruit kijken. Dit vergt een hoog aanpassingsvermogen.” Om snel te reageren op een spoedopdracht, een kapot product of een storing zorgt STT ervoor dat de fabriek altijd een overcapaciteit heeft. Dit is een opmerkelijke strategie van het bedrijf, dat ervoor heeft gezorgd dat er steeds meer toeleverwerk wordt aangetrokken. Een optimaal en flexibel productieproces vraagt om dito machines. Zo heeft de L230 LMSA CNC-draaimachine van Hyundai-Wia onlangs zijn intrede in het bedrijf gedaan.
’ONE STOP SHOP’
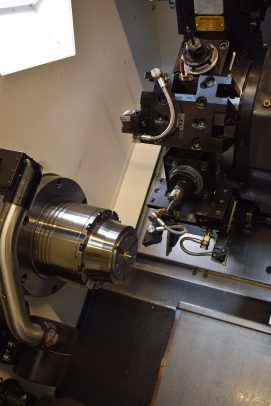
Het in september 2016 geïnstalleerde Hyundai-Wia L230 LMSA CNC-draaicentrum wordt als allrounder voor zowel bemande als onbemande productie gebruikt. Voor onbemande productie is het draaicentrum met een stangenlader uitgerust voor verspaning direct vanaf de staf. Dit maakt 24 uurs productie mogelijk. Daarnaast biedt de turret met 24 (aangedreven) gereedschappen, de subspil, het hoge vermogen (15 kW op de hoofdspil en 5,5 kW op de subspil) en de grote doorlaat van 65 mm aanzienlijk meer mogelijkheden dan de Hyundai HIT die na twintig jaar trouwe dienst plaats heeft gemaakt voor deze L230 LMSA. Werkstukken komen nu volledig afgewerkt uit de machine. Nog een cruciale eigenschap van het draaicentrum is de thermische stabiliteit; er zijn daarom geen meetlinialen nodig. “Een andere draaibank in onze werkplaats is pas na drie uur thermisch stabiel. Dit is een groot nadeel bij onbemand produceren. Het eerste werkstuk had een andere afmeting dan het laatste werkstuk dat van de machine kwam. Dat wilden we met de nieuwe machine absoluut voorkomen”, legt Woudstra uit. Door de betrouwbaarheid van de eerste Hyundai HIT heeft STT weer voor een draaimachine van Hyundai-Wia gekozen. Enerzijds door de mogelijkheden en eigenschappen van het nieuwe draaicentrum, anderzijds door de goede service vanuit de Nederlandse vertegenwoordiging Dymato uit Veenendaal. “Een machine is zo goed als de service er op”, benadrukt Kooistra. Willem van Dam, sales manager bij Dymato voegt daaraan toe: “Omdat Dymato een slanke organisatie is en we onze monteurs alleen inzetten voor onze klanten, kunnen we snel en wanneer nodig een monteur langs sturen.” Inmiddels kan STT zeggen dat dankzij de ingebruikname van de Hyundai-Wia er meer nieuwe orders binnenkomen.
Oplossend denkvermogen
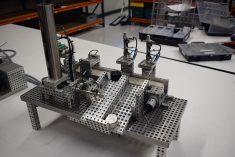
Voor de ontwikkeling van unieke machines en installaties maakt STT Products gebruik van het zelf ontwikkelde System 125. Dit is een soort ‘Meccano’ voor professionals waarmee het bedrijf miniatuur prototypes van elektrische/mechanische systemen kan maken. Vooral bij de ontwikkeling van compleet nieuwe oplossingen draagt dit bij aan het snel verkrijgen van een productontwerp. Tevens kan de klant direct zijn concept installatie zien en voelen. STT geeft aan dat bij werkzaamheden die nooit hetzelfde zijn, veel behoefte is aan werknemers die meedenken in oplossingen. “Dankzij onze werknemers die allemaal oplossingsgericht zijn, kunnen we snel construeren en produceren. Daar ligt een cruciaal verschil ten opzichte van de concurrentie, ook vanuit lagelonenlanden.”, vertelt Kooistra. Als voorbeeld noemt hij een draadloze headset waar STT nu productiemachines voor heeft ontwikkeld en gemaakt. De vraag vanuit de klant was om deze headset 30% kleiner te maken. In Azië, waar de headset eerst werd geproduceerd, konden ze hier met het handje niet aan voldoen, het was simpelweg te klein. Bovendien zou de kwaliteit er onder gaan leiden en zou er te veel uitval zijn. “Door slim te werken en met een hoog engineeringvermogen kan veel werk weer terug naar Nederland gehaald worden”, besluit Kooistra.